Over 60 diverse builds later, which homes did UK host Kevin McCloud pick as the best of the best?
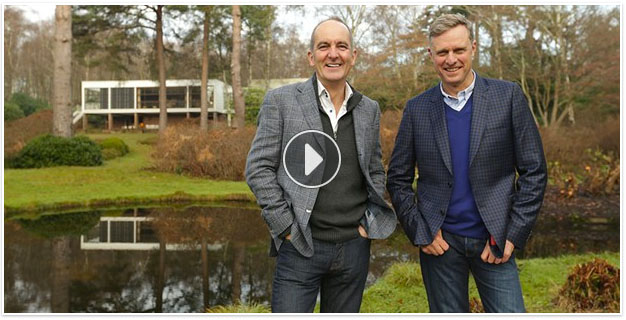
The top 10
Saturday 1pm-4pm,
Sunday 1pm-4pm
Tours at 1pm, 1:20, 1:40, 2, 2:20, 2:40, 3, 3:20, and 3:40pm – Booking required
Bookings open Monday 18 July 8:30am until booked out.
For tickets visit: https://www.eventbrite.com.au/e/5×4-hayes-lane-project-tickets-26262774666
The arrival of home storage batteries in Australia is likely to make renewable energy a more attractive proposition for householders, writes Katie Cincotta.
It’s been a long time coming, but finally we have some photos to release. The 5×4 Project building scrubs up very nicely, lighting up in the foreground in a city-scape at night, and absorbing plenty of solar rays during the day.
Willow Aliento, from The Fifth Estate, has written a follow-up case study on the 5×4 Project, providing a conclusion to the initial write-up by Cameron Jewell back in May 2013.
The Fifth Estate is one of Australia’s leading online newspapers in the sustainable built environment, providing free online journalism to all.
Please have a read, and check out the initial case study (the link’s in the article) as a reminder of the Project’s conception more than 2 years ago!
With the Grand Designs episode due to air, we invited all the Project Partners to come and celebrate the completed 5×4 Project construction.
For many it was the first time they had seen the building in its completed form, and the 5×4 Building certainly put on a show! The episode was played on the front façade of the building, while people stood and took in the building showcasing its own construction.
With the confined space, the Kitchen had to be able to transform into a Living room, and vice versa.
The TV unit pops up in front of the window – meaning that it can be a bench by day and TV stand by night.
The couch/kitchen table was designed by Ralph Alphonso and built in collaboration with 2nd Chance Tables, using recycled timber to construct the beautiful tabletop.
The table sits as the backrest for the couch, and pivots on a pin into a comfortable sofa. The stools transition between table chairs and footrest, and it is upholstered by Martel Upholstery with the fabric from Woven Image.
The Hot Tub up on the roof is finally ready to go, and doesn’t it just look fantastic!
Just like the theory of the rest of the house, it has the ability to be a cool plunge pool in summer, and a steamy spa during winter.
The cedar smells wonderful, and the Hot Tub from Ukko Hot Tubs that was installed so long ago is now in full use.
Efficiency Matrix were integral to testing the 5×4 Project for air tightness.
We were aiming to hit standards developed in Europe by Passive house. One of these tests involved a Blower Door Test – stay tuned for the results!
Here is a bit of information on Diamond Energy, our energy retailers that are up to a whole heap of good.
Dyson have come on board with the Project, supplying us with a V6 Absolute Handstick Vacuum! The V6 Absolute from Dyson is the perfect vacuum for the small spaces of the 5×4 House
Ralph recently had an interview with Giles Parkinson, from One Step Off The Grid, about the 5×4 Hayes Lane Project and his zero carbon lifestyle.
Please click on the picture below to read the full article, or head to their website: onestepoffthegrid.com.au
The Mechanical systems are a very important component in the 5×4 Project building. This balanced mechanical system provides us with fresh, filtered air all year round, and can recover up to 95% of heating and cooling throughout the building. The components have all been carefully chosen to work in harmony wiht each other, creating the most efficient and sustainable system possible.
(more…)
With the long process of this spectacular build complete, owner/builder Ralph Alphonso discusses how he feels living and working in the new space. With the limited space, there are a few lifestyle modifications to be made!
For more videos head to our Youtube channel: BarleyStore
The Build is nearing completion, and Ralph takes us through the final stages of the interior designs. Final finishes and commissioning were all being run, which again required more sequencing!
For more video interviews head to our YouTube channel BarleyStore for the full Construction Diary Interviews playlist.
Balustrades:
Staircases make up the main traffic ways around, up and down the 5×4 building, and with that comes necessary safety precautions. This generally means installing bulky balustrades to keep people slipping off the edges, however within our tight space this would have reduced the sense of space between floors within the building.
The solution? Glass Balustrades.
These are made with heavy-duty glass, and attached around the stairs.
All the appliances are now installed and ready for action. It is quite a slick line up, every appliance fitting into the contemporary design of the compact ecosystem. Here’s the list:
(more…)
Our Wall Systems comprises of 12 components – all doing their bit to conserve energy.
Both on the inside and the outside of the Wall System is Zero VOC Paint and Stain. Most paints or stains release toxic emissions into the air even after that ‘new paint smell’ disappears. These toxins are VOCs, or Volatile Organic Compounds, which improves the performance and longevity of paint. Until recently, these were essential to the manufacturing of paint, however our fellow environmentalist consumers have demanded the development of low-VOC or zero-VOC paints and finishes. Companies have refined their formulas, and are producing finishes that are as cost effective and durable as VOC paint, but also less harmful to the environment.
The stain drying
Whilst the difficult stage of fitting the services is taking place, Ralph goes through the custom furniture and the various lighting techniques around the build.
For more video interviews head to our YouTube channel BarleyStore for the full Construction Diary Interviews playlist.
One of the final exterior things to happen on site is the bluestone paving around the building.
Hayes Lane itself is heritage bluestone pavement, and the Melbourne City Council has worked with the 5×4 team to repave the area of the lane in front of the building.
As the 5×4 building uses every available piece of space, this means that this iconic Melbourne bluestone is paved right to the front door!
The Upholstery for the couch is in progress, so we went down to Martel to see what they were up to. See the video below, or head to our YouTube channel BarleyStore for the full 5×4 Hayes Lane Project playlist.
The Thin Tank has been installed. These tanks are a great option when wanting rainwater but not having room for a tank. The 5×4 building has about a meter between it’s wall and the neighbour’s, which is all the Thin Tank needs!
Installation was not a walk in the park, however once installed the tank melts into the design.
With the offsite construction of the custom designed bed, it was time to install it in the future bedroom of the 5×4 Building. This had to be done early before the stairs had balustrades installed, because it wouldn’t fit otherwise!. See the video below, or head to our YouTube channel BarleyStore for the full 5×4 Hayes Lane Project playlist.
The Geothermal system has finally been completely installed!
What began long ago with drilling holes into an empty worksite, has finally had the finishing connections put in and is blowing both hot and cold air throughout the house via the modest ducting and vents!
The queen size bed base for 5×4 has been installed in the 2nd floor. Of course, with space at a premium, it’s been kitted out with as many storage units as it can hold. Bit by bit, the 5×4 Buiding is taking shape.
The Couch/Dining room table has been custom made to fit the building.
The piece had to be compact and needed to be used as both a couch and a table. The solution was a roll-over design, created by owner-builder Ralph. Both Ralph and 2nd Chance Tables built the piece of furniture together.
The fabric for the couch and pillows were supplied by Woven Image. The couch fabric is 100% wool, and Comer and King chose the black and blue colours of the piece.
The indoor walls of FivexFour are currently being painted in white using Ecolour paint.
The painted plasterboard contrasts with the timber creating a clean and homely atmosphere.
The TV has been installed into its hidden storage unit.
It rises up from under the bench in the kitchen/living area – another effort to save space!
When the TV is out it dominates the space, so it is nice to be able to tuck it away during social dinners or breakfast!
Pop-up TV
The plaster put on the exterior wall of the neighboring building has been painted black with Ecolour paint to return the building back to its original aesthetic.
Along with the images we took of the stonemasons working on Hayes Lane, we also recorded some footage for our Video Diary. See the video below, or head to our YouTube channel BarleyStore for the full 5×4 Hayes Lane Project playlist.
The lights of 5×4 have been turned on for the first time. They are extremely energy efficient, with an entire floor calculated to use only 24W/hour. They operate not only via switch but also with a separate dimmer, so the brightness of the lights can be set and kept. The strips of lights fit into the wood create a sharp, modern aesthetic.
The site is getting busier, and the services are being fitted off, Ralph talks about the challenge of working and sequencing this stage of the build. The solar panels have all been mounted, but not without some help from some very specialised lifting equipment!
For more video interviews head to our YouTube channel BarleyStore for the full Construction Diary Interviews playlist.
The plants brought some fresh live to the construction site. See an installation video below, or head to our YouTube channel BarleyStore for the full 5×4 Hayes Lane Project playlist.
Today Creative Earth Landscaping planted the edible plants into the planter boxes provided by Décor. They then assembled them into the window sills according to a plan worked out by Phil Withers, a landscaper who focuses on edible plants.
Our little building, the 5×4 Project, is starting to look like a home!
The screens have been installed. In the bedroom they’ll be used to block light and provide privacy, while on the deck level they’ll also shield the wind.
The flyscreens have arrived and are gradually being installed.
Being such a tight build, windows are a important part making the 5×4 building feel spacious, even more so when they are open. Flyscreens will help keep bugs out while the windows are open. They were also made by Paarhammer to fit the windows exactly.
Sam from Creative Earth Landscaping and Phil Withers (Phillip Withers Landscape Design), met today at the 5×4 site and made some planting decisions about which edible plants will go where and in what order within the 5×4 planter boxes.
While Phil Johnson (Phillip Johnson Landscapes) designed the garden with the help of Phil Withers, Sam will maintain the plants in the coming weeks and educate Ralph on how to best care for them.
Phil Withers, collaborator of Phil Johnson Landscapes, talks with Sam from Creative Earth.
With a second coat of dark stain being applied to the wooden floors, stairs and bench tops, the patterns in the ASH timber are starting to come into their own.
The stain comes from a dilution of stainless steel soaked in vinegar. Don’t be fooled by the simplicity though – it’s quite hard to apply uniformly, but Timber Care were a match for the task.
It was time for the side solar panels to be installed on the western wall of the building, to make up for the lacking roof-top space.
Alfasi Hire took up the challenge in providing one of their many machines for hire, which needed to be able to fit down our little lane way whilst still being able to reach up and around the 5×4 building.
The floors received a (rather noisy) wire-brushing from Timber Care, which scrapes away any soft wood, leaving hardwood behind for durability and the smooth finish of floorboards.
Over the past few weeks there has been focus on the electrical side of things, with wiring being installed on all four floors by The Torus Group.
This electrical stage has been more complicated at FivebyFour than the average build because a number of extra products are being installed, including an energy monitor, DAS Home Security and Yingli Solar Panels.
It’s a slow and difficult process. Not only dealing with large amounts of tangled wiring but also working with the delicate membrane of the wall systems in an effort not to effect the airtight factor of the building.
Timber Care came and experimented with a number of stains. We finally settled on using the darkest stain for our kitchen bench tops and floors, which is made from vinegar and steel wool stain.
For the eco-plywood cabinets, Timber Care used a white diluted concentrate as an undercoat to ensure the oil wax did not yellow the colour of the wood.
After the stains, hard wax oil is applied to make the wood waterproof. This is particularly important for the bathroom, which has wooden benches. Unlike varnishes, the hard wax oil does not need to be sanded to be renewed.
The Geothermal Heat pump system is being set up by Direct Energy. The heat pump and compressor are being instated and connected to the geothermal pipes. Ventilation ducts are being weaved through the walls to all four levels.
The Geothermal Heat Pump System will cover the heating, cooling, hot-water and ventilation of the 5×4 building.
Water has been added to the hot tub, completing the final step of the installation.
The tub, crafted by Ukko, is designed to leak for the first few days until the wood expands and fills in any gaps.
With water in the tub, the smell of the wood is filling the top level of the build. The tub has a corona discharge ozonator and an ioniser which means the water will have minimal chemicals.
The lifestyle appliances are being installed, and the garden planter boxes are bringing a bit of life to the construction site.
For more video interviews head to our YouTube channel BarleyStore for the full Construction Diary Interviews playlist.
An enlightening visit to the Coolon LED factory left us seeing stars this afternoon.
With their impressive light display and their (relatively) low power bill, these lights are going to be perfect for the 5×4 building.
Pretty much no heat, compact designs, and bright futuristic designs – these lights will feel right at home!
Over the slow months around Christmas and New Years, The 5×4 Building finally gets to lock up, with the glass and plaster being installed. Inside, the cabinetry is starting to take shape, immediately making the space feel more like a home.
For more video interviews head to our YouTube channel BarleyStore for the full Construction Diary Interviews playlist.
The all-important bathrooms are being installed and tiled. The en-suite bathroom is now beginning to look like a bathroom, having been kitted out with a shower head, sink, taps, and a toilet. The downstairs bathroom is a complete wet bathroom, meaning that it is waterproofed and tiled all the way up to the ceiling.
Chriscol Kitchens have started installing the kitchen cabinetry on the second floor.
This is made up of FORMrite Plywood from Carter Colt Harvey, with a black finish and an exposed edge.
The raw look of the plywood on the black finishes look fantastic, and is just waiting for the wax treatment to finish it off.
Rayson RTK is working with our 5×4 Team to construct the important ducting system.
These ducting pipes will allow the building to circulate air, working to keep the air fresh whilst still maintaining a stable temperature in every room.
This particular product is called RAYFLO, and is easily customizable to suit our unique design.
The crew from Just Stairs came around to install the hardwood stairs.
Just Stairs have worked with the 5×4 Team to first design and construct these three sets of stairs, working with hardwood timber that ASH supplied.
Once cut and shaped, the installation team from Just Stairs fitted these custom made flights whilst Grand Designs watched on.
With our small footage and tall height, these stairs are very important for the accessibility of the house, but also aesthetically, as they take up a almost a quarter of the space within each room.
It’s no use trying to create an airtight home if you don’t know how airtight it actually is!
To help us find out how we had gone as far as making our building airtight, John from Efficiency Matrix came round to conduct a Blower Door Test.
On the base of our garden boxes we used waterproofing materials from Mapei so that the boxes would not deteriorate when exposed to the elements or buried under a bit of soil.
For this ‘tanking’ process we used two different products from Mapei, an international company specialising in adhesives and sealants. (more…)
It’s finally time for the glass on the east facade to be installed!
With the help of a scissor-lift, the Audsley Windows installers attached the 10 ft pieces of class to the frames, while Grand Designs got it all on camera.
Another truck driver did extremely well to reverse down the lane and deliver the Fiberock Aqua-Tough plaster boards from USG Boral.
Once the measurements have been taken, these boards are being cut to size and then installed over the building.
As with the body care and cleaning products, the fabrics used in the 5×4 Project play an ongoing roll in the building’s environmental impact. One of these fabrics currently being tested is woven bamboo towels and bed linen, supplied by Bamboo Village.
Why bamboo? (more…)
The first round of Solar Panels have gone up on the 5×4 Building.
With the structure complete, Ralph explains the complex Wall System that is going to keep the 5×4 Building at a stable temperature. (Also includes a quick time-lapse of the luxurious rooftop hot tub being installed on an unusually rainy day!)
For more video interviews head to our YouTube channel BarleyStore for the full Construction Diary Interviews playlist.
A quick time-lapse of the hot tub being installed. due to its size and weight it had to be installed very early on in the build. See the time-lapse below, or head to our YouTube channel BarleyStore for the full 5×4 Hayes Lane Project playlist.
It was time for the pressure-treated exterior cladding from ASH to go up as the final section of our Wall System.
Long 5 meter planks were passed up the scaffolding to be nailed into place, interlocking each other to create the water-tight finish.
The process of air-tightening the building has begun!
On top of the external layer of Spaceloft insulation sits the Pro Clima, the exterior airtight layer as advised by Passive House Australia.
This was boarded roughly in place, and then taped at all the edges and joins to create an airtight wrap around the whole building.
On the exterior of the building we tacked a layer of Aerogel‘s Spaceloft, a compressed insulation blanket capable of protecting against temperatures between -40 and 200 degrees Celsius.
The insulation began to be stuffed in around the frames on the inside of the building.
The first layer of insulation inside was the insulation batts. We had a mixture of RAMS’s part-wool-part-recycled-polyester batts, and GreenStuf’s 100% recycled polyester batts.
The windows have been installed on the rear (west) side of the building. The windows, made and glazed by Viridian, and framed by Paarhammer, are built to be airtight, like the rest of the house. This means sturdy latches and tight seals.
They will endeavor to keep the afternoon sun at bay, but will need some help from the blinds that will be installed in the next few months!
Due to our incredibly small square footage, a garden looked impossible to incorporate. We decided to have garden boxes on the west facing side of the building, utilising the space in the wall.
Having it on the west wall served two purposes:
Firstly, the plants need sunlight to survive, and the afternoon sun will set over Melbourne and during summer they will get full sunlight for about 6 hours a day.
Secondly, whilst the sun brings life for the plants, it also brings unwanted heat to the building, and the inset garden boxes help with absorbing that sun as well as shading the windows from the direct sunlight.
5×4 has had the very exciting news of being picked up by a T.V Show. While we can’t yet confirm the details, the program has chosen 5×4 for its unique, innovative design and will follow the build of the house.
The program is set to air in the second half of 2015, so keep your eyes and ears open!
Our humble 5×4 Project has developed more global momentum this week after being presented at the World Sustainability Conference (WSC) in Barcelona. A case study on the project by R.H. Crawford and T. Hollingsbee was presented, which assessed the Embodied Energy of our building, and how we have optimised its energy performance. The Embodied Energy is the consumption of energy over the lifespan of the building, including construction, materials manufacturing, and of course recurring energy costs – such as appliances etc.
The case study and resulting presentation looked at measures that the 5×4 project had taken to substantially lower the embodied energy of the building, and using environmentally friendly materials and appliances, building consciously for minimum energy consumption, and finally generating green electricity through solar power to cover the remaining energy costs.
Click here to download the complete paper, or visit the WSC website for more about their sustainable ambitions and their next conference in 2017.
Ukko has arrived with the hot tub. The hot tub itself is made from Canadian Western Red Cedar, and the crew from Ukko hoisted it up to the roof in pieces, assembling it once it was up there. Completely handmade, it is just asking for the rooftop deck to be built around it.
Torus Group installed the solar panels on the test site today, in an effort to offset the emissions of the build. This meant our test site would be generating enough power to effectively make the build carbon neutral, fitting in with our project mantra.
With a lot going on, Ralph runs through the busy month of October. The progress is impressive, from a site of foundations to a fully constructed building! One of the many perks of prefabricating wall, floor and roof cassettes!
For more video interviews head to our YouTube channel BarleyStore for the full Construction Diary Interviews playlist.
In just three days we had the whole 5×4 structure up, with everyone working in sequence to make sure it was a smooth process. See the video below of all three days, or head to our YouTube channel BarleyStore for the full 5×4 Hayes Lane Project playlist.
Day two of the prefabricated installation went rapidly. The third and the fourth stories were assembled, the riggers doing a fantastic job to get all the pieces up there by crane safely and in one piece.
On the final day of the assembly the third story and rooftop went up, completing the assembly process. The final piece was the wooden beams that create the ‘roof’ of the rooftop hot-tub.
The day has come! The walls, floors and roof arrived, with the truck driver from DWTT reversing down our narrow lane-way with his semitrailer.
Melbourne Cranes set up their crane, and began to lift the layers on top of the hollow block work. As with most prefabricated things, we hit a bit of a snag on the first layer, and had to make a few minor adjustments to the first roof/floor, but after that it began to go up smoothly.
Because we were having all the walls, floors and roof prefabricated off site, it meant the plumbing for the roof also needed to be done off site.
To allow for the rooftop deck to be laid over the top, Design Sheet Metal supplied a Custom Stainless Steel flat roof.
With another trip up to Drouin, we helped the guys from Atherton Plumbing waterproof and install the roof on the prefabricated wooden frame.
The off-site construction of the prefabricated wall and floor panels all happened at Druin West Timber and Truss. We went up to take a look, so see the video below, or head to our YouTube channel BarleyStore for the full 5×4 Hayes Lane Project playlist.
Once the slab was down and set, it was time for the breeze-blocks to be laid for the bottom story of the build. These blocks are hollow, and are filled with E-crete for extra stability.
Whilst the site is being prepared for the concrete slab, Ralph and the 5×4 team head down to discover how the Vic Ash hardwood is being cut and treated. Once site preparations are complete, it is time for the slab!!
For more video interviews head to our YouTube channel BarleyStore for the full Construction Diary Interviews playlist.
Pilacon did the final preparations to the site for the concreting, and Grand Designs set up to film the pouring of the slab. Ralph had a chat to them about the eco-friendly concrete – or e-crete – we are using.
E-crete is a product offered by Aurora Construction Materials (ACM) that is environmentally-friendly and possibly ‘the greenest’ concrete used anywhere in Australia.
Replacing conventional cements with waste materials from industrial processes, E-Crete produces up-to 80% less carbon than conventional concrete. For more on e-crete and ACM, visit out Project Partners page.
ACM brought in the e-crete, and began to pour the slab. Within two hours the slab was poured, and the guys from Pilacon finished it off by early afternoon.
Head to our YouTube channel BarleyStore for the full 5×4 Hayes Lane Project playlist.
Before the concrete arrived it was important to prepare the plumbing and boxing and make sure that everything was in the right place. The team from Atherton began to lay all the pipes and the Pilacon guys began to build the boxing for the slab. When the steel delivery arrived the mesh was cut to size and installed in preparation for the concrete. See the time-lapse video below, or head to our YouTube channel BarleyStore for the full 5×4 Hayes Lane Project playlist.
First thing in the morning Stewart from Direct Energy came to connect the geothermal loop. The team from Pilacon, as well as the the plumbing guys from Atherton Plumbing arrived to connect the pipes and dig the required trenches in preparation for the boxing of the slab.
At the bright and early time of 7am, the excavating and drilling of the holes for the bored piles began. Once we had nine holes, each at 3.5 meters deep, the piles – or cages – were dropped into the holes. The concreter then filled the holes around the cages, leaving us nine piles concreted in place, and a site ready for the boxing for the slab!
Whilst on the topic of timber we met with Lew from Fisher Timber Preservation. We spoke about the different water-based pressure treatments for the hardwood, which treats hardwood to be similar to treated pine in terms of durability and weather proofing.
Whilst up in Drouin we met with Daniel Wright from our project partner ASH to discuss hardwood samples over lunch. We got a briefing on ASH in general, covering their sustainability measures and their process. We followed that up with a tour through the timber mill.
After a long drive up to Drouin, we met with Andrew and Paul from Drouin Timber and Truss about the floors, walls and windows for the 5×4 project. We were there to refine any variations to the prefabrication plans for the project, as we didn’t want pieces of the puzzle arriving on site that didn’t fit the rest of the building.
Ralph takes us through the various site activities such as geothermal digging and drilling, as well as running power and water services to site. Meanwhile product testing has begun, with a energy efficient dryer and natural ranges of cosmetics and cleaning products in use. For more video interviews head to our YouTube channel BarleyStore for the full Construction Diary Interviews playlist.
The eco-friendly laundry dryer by Asko was delivered for testing, with higher energy efficiency and less energy consumption. The old dryer in the test site was replaced by this dryer, which is more energy efficient than boiling a full kettle, meaning less cups of tea and more loads of washing!
Paul Stephenson from Stephenson Transport dropped in to discuss the transport schedule for Drouin West Timber and Truss. We also had to make sure the trucks would fit down our secluded little lane!
Ralph also met with Phillip Johnson from Phillip Johnson Landscapes helped brainstorm landscape ideas for the 5×4 project over a cup of tea.
The team from Webster Survey Group arrived on site, measuring up the property boundaries and the specifics for the concrete slab.
The electricity used in the build of 5×4 will be supplied by Diamond Energy and will be 100% GreenPower, sourced from GreenPower-accredited biogas generation plants at Shepparton and Tatura.
By purchasing GreenPower, households and businesses commit their electricity providers to purchasing the equivalent amount of electricity from accredited renewable energy generators, helping build renewable energy infrastructure and sources.
Please help us tip the scales in favour of renewable energy!
See either:
Over the course of ten or so days, companies MAXA Plumbing, Telstra and Power Cor laid the pipes for the installation of the services. This includes electricity, water, sewage, phone, data and television.
With preparation going on both on and off site, Ralph updates us on the progress of the build – finalising plans, designs and budgets. With the budget blowing out of proportion, some changes need to be made… For more video interviews head to our YouTube channel BarleyStore for the full Construction Diary Interviews playlist.
5×4 Hayes Lane Project & ASKO Appliances partner on the project to prove high quality can mean low energy!
The motivation for the 5×4 Hayes Lane Project is to construct a dwelling utilizing a small footprint of land. The space is to be liveable, functional and aesthetically grounded in a contemporary design. The engineering and materials in this project should be celebrated and on show. Living sustainably should not mean compromising on quality and The 5×4 Project aims to challenge such existing perceptions and encourage us all to embrace greener living.
Bringing together various specialists in their respective fields to contribute to the success of achieving these goals, 5×4 reaches out to ASKO, partnering to explore their high quality technology that employs lower levels of consumable energy.
Click below to read the full article and discover more of ASKO’s innovate technologies:
With the site cleared, the drilling teams from Direct Energy and Terra Test arrive, ready to begin the first geothermal drill. This is the first stage in the installation process of the heating and cooling system designed by Direct Energy.
Before the 5×4 building could be constructed, the old shed had to be demolished. See the demolition video below, or head to our YouTube channel BarleyStore for the full 5×4 Hayes Lane Project playlist.
With the plans organised, the day has come for the old shed to be demolished. With help from his brother-in-law Nick Lawrence, Ralph dismantled the shed, clearing the site for the project to begin. Part of this involved breaking up and then removing the old concrete slab, a task best undertaken with earmuffs!
Today marks a major milestone in the 5×4 Hayes Lane Project: the reception of the signed and approved Architectural Plans from the building surveyor. This exciting events propels the 5×4 Project onward into the building phase – FULL STEAM AHEAD!
Coming up next= Demolition of the shed and the existing concrete and laying the groundworks for the Geothermal Heating.
WellBeing Mazagine May/June Issue #105 – “Less Space, More Living”
With the ever increasing wave of interest in ‘Smaller Living,’ WellBeing Magazine engages with a series of projects striving for a sustainable lifestyle and connecting with their environment on a personal level. Questioning both the integrity and the practicality of downsizing, WellBeing writer Jo Hegerty, challenges our sizist natures and asks Ralph Alphonso whether less can in fact be more.
Click on the image below to download the full article:
Innovative Australians: Ralph Alphonso
BY Fiona MacDonald
Ralph Alphonso is showing that individuals can reduce their impact in a big way, with some planning and commitment.
On a 4 x 5m Plot down an East Melbourne laneway, Australian Geographic photographer Ralph Alphonso is attempting to build a liveable apartment on a leftover slab of land.
“I was going to build a garage or an extra room but I live here by myself and I thought, ‘Do I really need this space?'” he explains from his current living room, which has twice the floor area of his soon-to-be-built home.
When he looked for examples of carbon-neutral buildings for inspiration, he struggled to find one locally that looked at the whole picture – including where products originated from and -lifestyle.
“I found it frustrating. A lot of architects were talking about what could be done, but I wanted to actually do it. Waiting for someone else to go first isn’t my thing,” he says, with a smile.
A hidden back alley in East Melbourne will be home to an intriguing initiative. This project is named after the physical
constraints imposed by the site: a plot measuring 5m by 4m. Nestled between existing buildings, a prefabricated residential dwelling to house two people will rise three stories from the plot.
The design approach minimises the building’s life-cycle energy demand through innovative systems, materials and construction techniques
It will be an example of how to build and live in a small space. It’s an approach that is familiar in urban populations with high densities, such as Hong Kong, Tokyo, and interestingly, Warsaw, where architect Jakub Szczesny claims to have built the world’s narrowest house, which is 122cm at its widest point.
Such an approach will inevitably be embraced in big cities throughout Australia. The space between buildings will become increasingly more valuable as a growing and aging population competes for land, housing and desirable inner-city living
Click on the link below to read the full feature article
It’s approx. 6:15am on 12th December 2013.
I am in the Qantas Lounge at Melbourne Airport on my way to Sydney
Leaving Home at 5:15am this morning on a last minute business tip had me stretched thin.
I had to put on a load of washing, make sure i locked the door/windows switched all the lights off… the list goes on.
After checking in and sitting down to have some breakfast in the Lounge, I was also able to have piece of mind regarding the lights and appliances at home. The system by Zoo Automation is installed and being tested for the 5×4 Project.
The short video shows how i am able to see what is on… then;
*switch off the ensuite exhaust fan… I couldn’t leave the window open!!!!
*take the TV/Stereo off stanby mode… Saving power.
*take the washing machine off stanby after the wash cycle… Yes, i remembered to put the washing on… Once again saving power.
The theory of automation systems in the 5×4 Project supporting sustainable lifestyle, is an easy connection for me to see.
I can’t wait to test more of the features of the Zoo Automation System.
Ralph Alphonso.
The Victorian Chapter of the Australian Institute of Architecture last week held an event at the 5×4 Hayes Lane Project Site in East Melbourne.
Under the Sustainable Architecture Forum, ‘Raising the Green Bar,’ the 5×4 Hayes Lane Project was presented to the attending members of the Australian Institute of Architecture.
Craig Chatman (ARKit, Project Architect & Builder) along with Ralph Alphonso (Barley Store & Client/Project Manager) presented to the AIA members, their perspective and insights on the Project.
“The 5×4 Hayes Lane build aims to combine different materials and processes to create the smallest eco-footprint, whilst providing the highest performance.”
In addition we are carefully selecting the most sustainable and environmentally friendly amenities and appliances as possible for the build.
Click on the image below to have a look at some of our ideas for the build and feel free to suggest other possibilities.
In the current issue of Australia Geographic Magazine a feature article ‘Six Global Megatrends,’ has included the 5×4 Hayes Lane Project as an example for one of the trends.
The 5×4 Hayes Lane Project has just been featured in an article by Siusan MacKenzie of the East Melbourne Jolimont community magazine. The project has the support and interest of the community.
Click on the image below to view the full feature!
The 5×4 Hayes Lane Project has just been featured in an article by Sarah Day of the habitat magazine published by the Australian Conservation Foundation.
Click on the image below to view the full feature!
Ari Phillips featured the project in the article “An inside look at living in one of the most sustainble cities- Mebourne Australia” origionally published on ClimateProgress.
The article has picked up and republished by CLeanTechnica,
CleanTechReport and RenewEconomy.
Click on the images below to open the full websites.
Pooran Desai, Co-Founder of Bioregional and International Director of One Planet Communities talks about ‘One Planet Living.’ and its relevance to the 5×4 Project. See the interview below, or head to our YouTube channel, BarleyStore, for more interviews!
We are getting closer to the final specifications for the project and with that the questions are flying thick and fast… What are the products we are to use? What materials? How do we decide? In any circumstance these questions are not easy to answer. The project team has weighed in where their areas of expertise lie and overlap.
Where possible we will be testing the products in the Barley Store Office, for compatibility of systems and functionality in real life context.
Zoo Automation products for the home controls and energy reporting have already started being installed and tested. Security system along with cameras will be next with the custom programming systems.
Meeting held on Tuesday 6th August – GHD offices Melbourne
A range of construction assemblies were selected based on optimised thermal performance and a selection of standard and low impact materials.
Eleven different floor assembly variations and 52 different wall assembly variations were considered.
The total life cycle embodied energy of these assemblies was calculated using a comprehensive hybrid embodied energy assessment approach.
This included the energy embodied in the materials/assemblies for the initial construction of the project as well as the energy embodied in replacement materials over an estimated building life of 100 years. Average material replacement rates were used.
Assembly embodied energy figures were graphed and compared.
Major points that arose from the discussion of the embodied energy assessment results included:
• Materials with a high recycled content are preferred as they tend to have a lower embodied energy compared to virgin material alternatives
• Longevity and durability of materials needs to be considered as materials with a low embodied energy but that require frequent replacement can be a poor choice, resulting in a higher life cycle embodied energy than more durable materials
• Solid timber products are preferred over manufactured/processed timber products
• The embodied energy of some insulation products can be significant
• The embodied energy of glass can be considerable and the need for double and triple glazing systems must be balanced with the level of thermal performance they can provide
• Double-glazed spandrel panels should be avoided considering their high embodied energy
• The importance of minimising the embodied energy associated with the building’s initial construction was highlighted. Energy expended in the future (for replacement materials and building operation) is likely to be less carbon intensive than the energy presently being used in the manufacture of materials.
It is important that by minimising embodied energy that the thermal/operational performance of the building is not adversely affected. The next stage involves assessing the life cycle energy/carbon implications of a smaller range of optimised assemblies, based on the knowledge gained from this initial analysis.
Dr. Robert Crawford
Senior Lecturer in Construction and Environmental Assessment
Click on the images below to open the full documents.
How is the Project schedule traveling?
“Well, I think we are in good shape. The previous schedule would have us close to completion at this point. I thought I would get that out of the way early…
We are currently in the final stages of specifications. (more…)
Click on the image below to open the full draft plans.
The project has been featured in an article by Cameron Jewell of TheFifthEstate magazine. The article introduce the building and the project manager Ralph Alphonso and especially refers to the featured best-practice passive design and advanced engineering techniques, which includes the areas:
CLick on the image below to read the full article.
Beyond Zero Emission featured us in their blog today.
BZE is assisting the 5×4 team with the specification of these electrical appliances and the zero fossil gas/ 100% renewable electricity project. The dwelling will be powered by a combination of rooftop solar photovoltaic and 100% renewable Green Power.
Click on the image below to view the full post!
The Project has been featured in an article by Sarah Day of ACF. Click on the image below to read the full article!
Today we interviewed Danny Vadasz, COO of Australian Conservation Foundation.
Issues discussed include:
– ACF’s work in urban challenges
– ACF’s contribution to sustainable building and how they support any project with similar aims on sustainability
– Defining success in build projects
Direct Energy is on board as one of our Project Partners. Direct Energy is both designing and installing geothermal heating & cooling solutions to provide energy efficient air conditioning and hot water for the Project. The animation below demonstrates a typical Direct Geothermal system:
Our interview with Professor Rob Adams AM, Director City Design at City of Melbourne. His thought on the 5×4 Hayes lane Project.
Rob was awarded the Prime Minister’s Environmentalist of the Year Award in 2008 and the Order of Australia in 2007 for his contribution to Architecture and Urban Design.
A champion of both the arts and environmental sustainability he has worked to ensure that good urban design is established as a platform for city development into the 21st Century. Some key projects include CH2 Australia’s first 6 Star Green Commercial Office Building, Birrarung Marr, Swanston Street, City Square, Sandridge Bridge, East Melbourne Library, Urban Forest Strategy and the City of Melbourne Street Furniture range.
His current interests concern the health and sustainability of the Metro city and he has published and presented extensively on the subject of Transforming Cities for a Sustainable Future.
The 5×4 Hayes Lane Project is supported by Beyond Zero Emissions (BZE).
Check out our interview with Trent Hawkins, BZE’s Project Director of the Buildings Plan.
Issues discussed include:
– How BZE works to investigate solutions to the current fossil fuel economy
– Why it’s important for BZE to associate with the 5×4 Hayes Lane Project
– The desired outcome from the Project
The Project Team met today to discuss the Embodied Energy of the 5×4 Hayes Lane Project. The total embodied energy of the Project will be measured and assessed by Dr Robert Crawford.
We discussed the challenges that would be met with measuring the embodied energy…
– The hardest part about the analysis is getting the quantities
– Assumptions can be made based on past knowledge but it wouldn’t be as accurate
– Also need to consider how much of each material goes into construction
– Specification of each material required (i.e. thickness, density) to make a better assessment
– Difficulty in comparing materials (i.e. How to figure out comparable quantities for different types of materials)
– Acquiring life-cycle assessments (LCAs) from the manufacturers of products used can be difficult
– Considering the build-up of materials, durability and the recurrent embodied energy
– Ensuring the energy savings is greater than the energy output
– How the design life for the build would affect the embodied energy
In the next few weeks, the Project’s Architect and Engineers will work together to come up with a detailed material analysis, with details about their quantum of area and volumes to be used in the Project. This will then assist Dr Robert Crawford in assessing the embodied energy, allowing for us to come up with the most ecologically friendly product and material solutions for the build.
We’ve drafted a timeline for the project, which you can view below. We are close to finalising the structure of the build and should be ready to apply for our building permit in June, 2013. If all goes according to plan, construction will commence early August, 2013.
Click on the image below to view the full Project Timeline:
Here’s a sneak preview of the 5×4 Hayes Lane building will come together… proposed by ARKit.
Images by ARKit.
Today we had a meeting with Craig Chatman (ARKit). At this point we are close to finalising the structure of the build.
Points of discussion included:
– Sewage/ plumbing issues
– Electricity
– Transporting the build
– Material analysis
The following were discussed during the material analysis:
– Walls –wall lining options (e.g. plywood, bamboo, cork)
– Flooring systems –floor structure options
– Internals & finishings –e.g. bamboo, plastic, paperock compressed paper.
– Kitchen appliances –fridge, dishwashers, oven, etc.
– Bathroom finishes
After considering all the possible materials, final decisions are yet to be made. With the help of our other team members, Tai Hollingsbee and Dr Robert Crawford, we’ll be able to compare the embodied energy of each product and choose the most eco-friendly one.
The performance of our building should be finalised by the end of this month in which we will have a clear idea of the materials and appliances that will be used in the building.
At this rate, we hope to begin construction August 2013. Stay tuned for future updates!
Prior to the construction of the build, we interviewed all members of the Project Team. Here’s the first interview with Dr Robert Crawford who’s in charge of measuring and assessing the Project’s Embodied Energy.
Issues discussed:
– Opportunities for minimizing the carbon and energy input of the Project
– The input-output based hybrid assessment approach that will be used for quantifying the embodied energy and emissions, which is more comprehensive than using traditional industry based process analysis techniques
– The benefits of the prefabrication approach used to construct the 5×4 Hayes Lane Project
– Other considerations for selecting construction materials, such as recyclable content
– Opportunities to showcase the 5×4 Hayes Lane Project to other design & architect students as an ideal outcome of the project
Watch Craig Chatman speaking about the design response of the 5×4 Hayes Lane Project.
Issues discussed:
– The design solutions of the mini tower
– The interesting dialogue between private and public realm of the dwelling considering it’s location
– The constraints of the build due to its small scale
– Being able to offer a design solution which talks about circulation, movement and flow
– Showcasing the engineering of the project within the structure of the building
Prior to the construction of the build, we interviewed all members of the Project Team. Here’s the first interview with Project Architect & Builder, Craig Chatman.
Issues discussed:
– An overview of ARKit & Offsite Constructions
– The importance of Sustainability, Design & Construction in the build environment
– The educational benefits and the contribution to the build environment as his motivation to get involved
– Examples of similar projects overseas
– The unique prefabrication solution for the 5×4 Hayes Lane build, made specifically for the site
– Constraints to the site due to limited accessibility and the Project’s scale
– The collaboration process of the Project Team
Tai Hollingsbee discusses the design philosophy for the 5×4 Hayes Lane Project.
Issues discussed:
– High performance building envelope
– Top-end technology and strategy to provide for the rest of the build’s systems
Prior to the construction of the build, we interviewed all members of the Project Team. Here is the first interview with Principal Engineer of GHD, Tai Hollingsbee.
Issues discussed:
– The paradoxical attitude on sustainability in Australia
– Why Tai Hollingsbee got involved with the Project
– How the Project addresses the issues of livability in cities and densification
– The Project’s unique ambition towards monitoring and accounting for its ecological footprint
– GHD’s unique integrated design service, which can optimize the design of the Project
– Challenges the Project might face, including public perception and financial viability
– A satisfied occupant as the desired outcome of the Project
Prior to the construction of the build, we interviewed all members of the Project Team. Here’s the first interview with Structural Engineer, Peter Felicetti.
Issues discussed:
– The economic benefits of sustainability
– Why Peter Felicetti got involved with the Project
– The holistic approach of the 5×4 Hayes Lane Project
– Implementing ‘Spanman’ into the design process
– The possible challenges due to the scale of the project
– The importance of good communication amongst the Project Team
Prior to the construction of the build, we interviewed all members of the Project Team. Here’s the first interview with Director of BioRegional, Ed Cotter, who will be helping us implement the One Planet Living principles into the 5×4 Hayes Lane Project.
Issues discussed:
– An overview of the One Planet Living principles
– Australia’s status on sustainability
– How Ed Cotter got involved with the Project
– Other projects using the One Planet Living principles
– Possible challenges with the 5×4 Hayes Lane Project
– The desired outcomes
Prior to the construction of the build, we interviewed all members of the Project Team. Here’s the first interview with Project Client & Manager, Ralph Alphonso.
Issues discussed:
– Ralph Alphonso’s role on the Project
– His inspiration for the 5×4 Hayes Lane Project
– Similar projects overseas and the lack of similar projects in Australia
– An overview of the Barley Store
– Possible challenges the Project could face including economic challenges and building challenges
– The desired outcome from the Project
On March 7th, 2013, the 5×4 Hayes Lane Project Team had a design and development meeting at GHD. Attendees included Craig Chatman from ARKit, Tai Hollingsbee and Chris King from GHD, and Ralph Alphonso from Barley Store. The main purpose of this meeting was to discuss the best combination of systems and construction materials to be used that would achieve the smallest ecological footprint possible.
Points of discussions were:
– the insulation system
– solar panels
– water/ irrigation system
– wood as construction material
Some of the possible technologies considered included:
– phase-change material (PCM) for heating
– rainwater collection as an eco-friendly water source
– hot water ring
– fake grass (e.g. summer envy)
– PV-cells
Overall, various materials and systems were brought to the table. The meeting saw even more opportunities for a sustainable build and the designs were further developed.
There are still various issues to be considered before making final decisions about the materials and technologies including:
– costs
– impact on infrastructure
– embodied energy
We will resolve these issues in future meetings.
(To see the sketches that were drafted at the meeting, click on the image below)
Click on the document below to download the Project’s Planning Permit, issued by Melbourne City Council.
The 5×4 Hayes Lane Project was presented at the Melbourne Forum, a series of free public talks with the goal of increasing the development and refurbishment of commercial buildings in Victoria to achieve greater levels of sustainable performance.
The 2012 series was based on One Planet Living and featured the 5×4 Hayes Lane Project as presented by mechanical engineer, Chris King, from GHD.
Click on the image below to view or download the full presentation by Chris.
Part rating tool, part eco-manifesto, part sustainability concept, One Planet Living aims to get us thinking about living within our finite resources, as Ecolibrium staff writer Rachel Urquhart discovers when she interviews Bioregional director Ed Cotter.
Ecolibrium is the official journal of AIRAH. It is read by over 10,000 professionals in the HVAC&R industry every month, and features the latest industry news, case studies on major projects, technical papers, information on the latest professional development opportunities available to industry and more.
Click on the image below to view or download the full article
On the 30th of April, 2012 the Project Team met to discuss the One Planet Living Principles.
Meeting objectives:
– To familiarize everyone with OPL principles
– Visioning session on what we want to achieve
– What the client will have to contribute and how it will impact their lifestyle
– Map out strategies around what we can put in place, what’s cost effective, how it’ll look at various stages of the project
We have drafted our strategies towards One Planet Living for the Project. Click on the image below to read the details!
Tai Hollingsbee, Principal Engineer at GHD was profiled by Architecture & Design and was proud to talk about his involvement with the 5×4 Hayes Lane Project.
Tai, is the engineer on the Project.
The project is already getting exposure internationally…
http://www.oneplanetliving.net/be-inspired/one-planet-living-map/
http://www.oneplanetcommunities.org/communities/applying-the-principles/hayes-lane/
And, was presented by One Planet Living to the United Nations at the Earth Summit 2012 in Rio, Brazil.
What a great way to get the ball rolling.
The 5×4 Hayes Lane Project first received international exposure when it was presented by BioRegional at the Earth Summit 2012 in Rio, Brazil.
BioRegional’s strategy is to work with partners on a number of projects that demonstrate One Planet Living, giving us a glimpse of what the future could look like and showing us how One Planet Living can work in the mainstream of our economy.
The Rio+20 Summit, held in June 2012, offered BioRegional and their partners an unprecedented opportunity to influence global sustainability policy and practice by showcasing the One Planet Communities and Businesses and their One Planet Living Framework, as well as contributing to the process itself. They highlighted key projects and organisation throughout the globe, including projects throughout the UK and Europe, in China and the US, as well as South Africa, Mexico, Brazil and Australia (5×4 Hayes Lane Project).
By 2015, they pledge to train 10,000 people to use One Planet Living. Based on the work of BioRegional and their partners to date and these fresh commitments, the UN Department for Economic and Social Affairs invited BioRegional to register One Planet Living as a recognised UN partnership, providing opportunities for One Planet Living information, case studies and toolkits to be made available via the UN’s online platforms. It also brings recognition and acknowledgement for the One Planet Living sustainability framework amongst UN agencies and governments.
Read more
Today reps from GHD and One Planet Living, Barley Store Productions and ARKit had an initial meeting to discuss the direction of the project, aims, visions and expectations. The results of the brainstorming session are on the printout below.
Some of the points of discussion were:
-Construction
-Operation
-Sustainable transport, food, water, materials
A Planning Permit Application has been submitted to the Melbourne City Council.